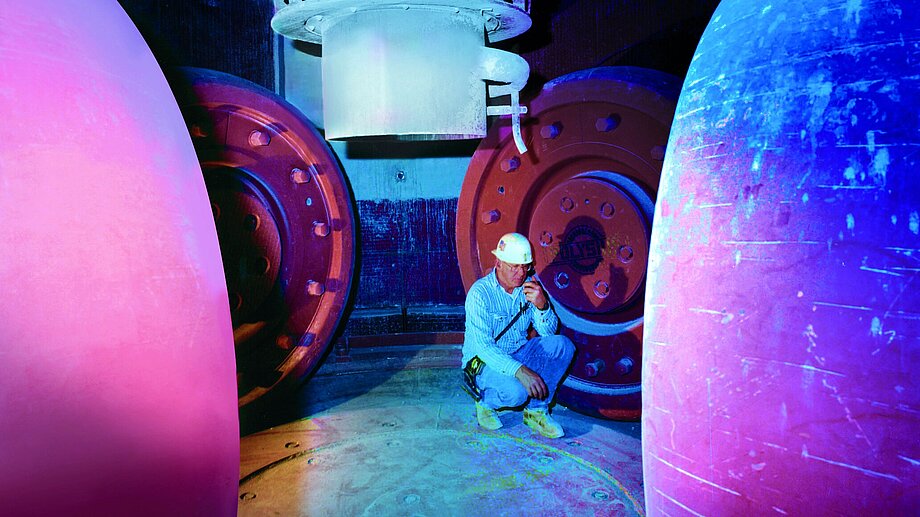
quadropol® - Vertical Roller Mill
We have decades of experience and numerous successful references in the field of mill technology. However, many of these mills are no longer in optimal condition after several decades of operation. Often, the reduced throughput of the mills also lowers the productivity of the upstream and downstream plant components, and the specific energy consumption is also significantly increased in the process.
Spare parts management
In the spare and wear parts business, we focus on shortening the unscheduled downtimes of our customers‘ plants and improving plant performance.
To achieve this, our team of experts examines the individual production processes and based on their OEM expertise and new material technologies, develops suitable wear part solutions for the respective application in combination with appropriate business models.
Thanks to our long-term experience as an OEM supplier, we can provide innovative spare parts concepts to meet your quality and performance requirements: on the one hand, the engineering and manufacturing of individual spare parts in line with your requirements; on the other hand, the ongoing development and enhancement of spare parts and components to increase the availability and performance of your plant. We also offer spare and wear parts for plants that were engineered and erected by third parties.
Highlight Services
- Wear plates
- Bearings
- Grinding rollers
- Sealing material
- Grinding table components
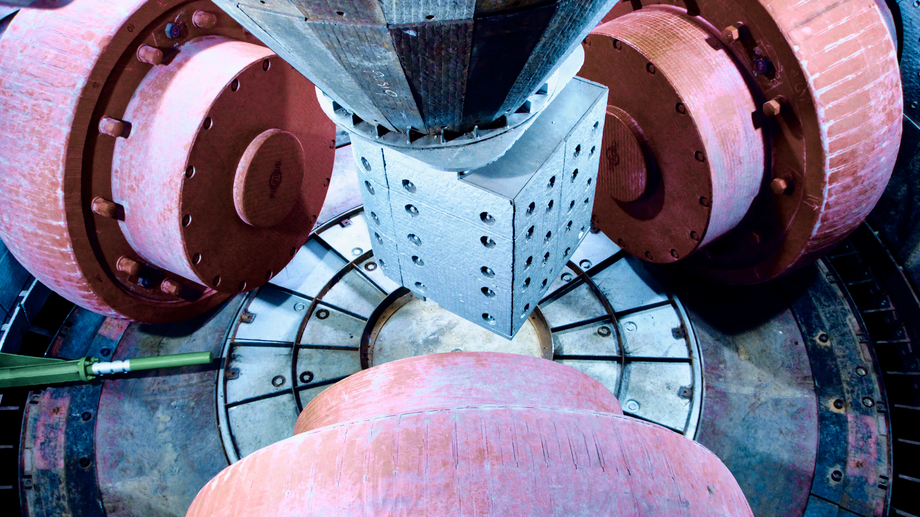
Modernisation measures
To achieve this, our specialists from the fields of process technology and mechanical systems, as well as service, analyse the entire mill system. In addition to the mill, they examine the separator, the coarse feed valve, the fan, the cyclone and the filters. We carry out measurements during operation and inspect the grinding compartment during a stoppage. This ensures a complete picture of the mechanical condition and the specific operating conditions of the plant. Following the analysis, clear statements can be made concerning for example, the grinding bed depth, the quantities of false air, the air velocity in the nozzle ring, the gas flow volumes or the wear behavior. On this basis, we can identify optimization potential for the plant and can usually increase both performance and availability. Together with your as our customer, we draw up a detailed emergency plan and put it into practice directly on site.
With the implemented measures, we can increase plant availability and boost productivity. The reduced energy consumption also lowers the operating costs.
Highlight Services
- dorol Expert Service
- quadropol® Expert Service
On-site services
Maximum availability of the system is crucial for economic success. To ensure this, we offer you various forms of inspection, repair and maintenance services by our trained specialists. Our offer includes numerous measures that can be carried out individually or combined according to your requirements.
Highlight Services
- Inspections
- Repair services
- Drive inspection
- Training
Digital services
Thanks to our state-of-the-art remote support tools, we are always close to you - even when you are far away. Our specialists provide you with real-time on-site support, whether it's for troubleshooting or regular maintenance. Using online live video support, we can transmit sounds and images of your work area directly to our experts. This allows us to check your system precisely - from your perspective - and thus support you quickly, effectively and, above all, inexpensively.
References
Cement Industry – La Cruz Azul
Lagunas/Mexico (Completion October 2012)
The quadropol® QMC is the latest roller-mill generation, which was developed especially for cement and granulated-blast furnace slag grinding. The turnkey cement grinding plant is designed for a throughput of 175 tonnes per hour.
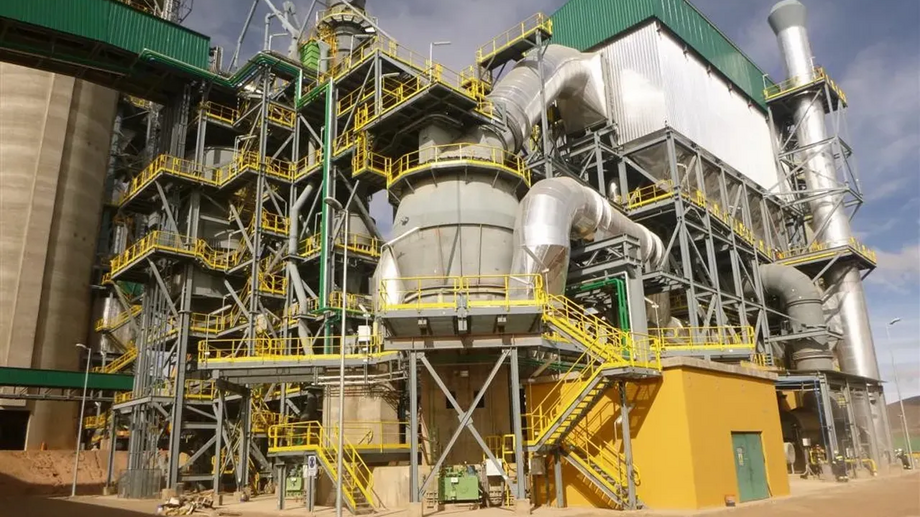
Cemento de Bolivia
Product References: quadropol® – Bolivia
Cementos de Bolivia ordered a 3,000 tons per day kiln line, successfully commissioned in 2019. This was an EPC contract to the German-Spanish polysius-Imasa-Valoriza consortium. The contract included a QMR² 38/19 for raw grinding and a QMC² 45/23 for cement grinding.
After the shortest time, the plant was able to meet the project’s design parameters, fulfilling all process/technical guarantees.
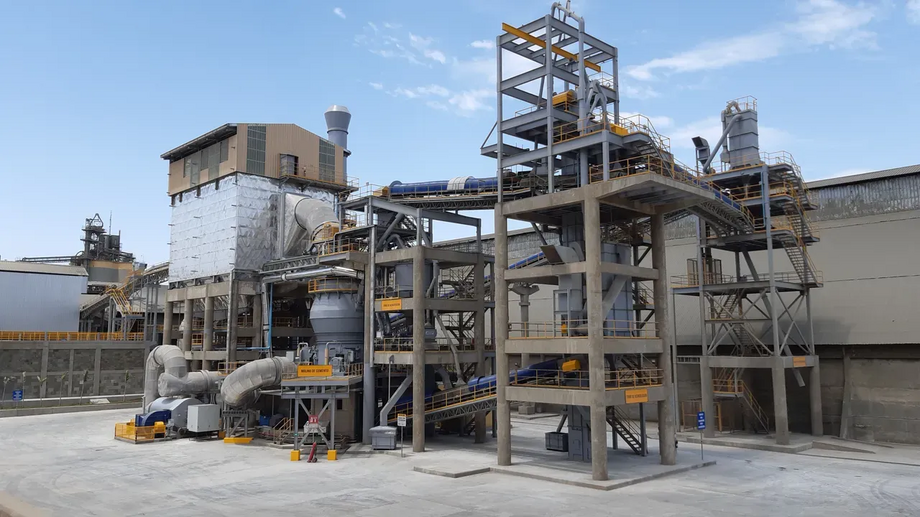
Cementos Cibao S.A.
Product References: quadropol® – Dominican Republic
Cementos Cibao S.A., cement producer in the Dominican Republic, continues the modernization process and ordered a cement mill type QMC² 40/20 for grinding different cement types. Compact plant arrangement with service tower, quadropol® vertical roller mill and main filter are part of the supply. Optimized mill operation will be supported by a digitalization package incl. intelligent mill controller. The mill is operating very successful since mid of 2021.
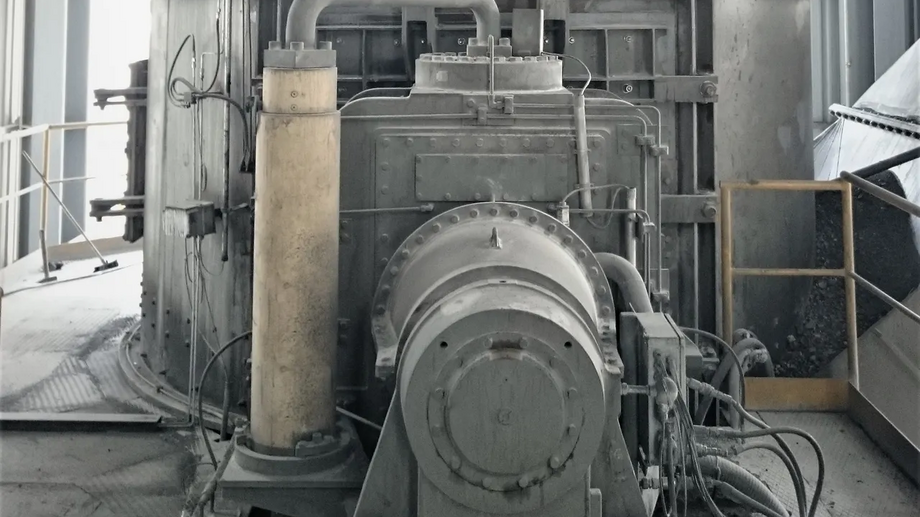
quadropol® – Kenia, India, Indonesia
Product References
The quadropol® concept for coal or pet coke grinding, with adapted table speed and high efficiency separator sepol®, ensures a safety mill operation and serves reliable the kiln burning process. Mombasa Cement Ltd. ordered a QMK² 24/12 with three roller units for the 5,000 tons per day kiln line. In addition, the raw material grinding process will be supported by a QMR² 48/24. For the 4,000 tons per day kiln line Shiva Cement Ltd. contracted a quadropol® vertical roller mill for grinding pet coke with a QMK² 32/16. The same mill size QMK² 32/16 is running in Indonesia for years now, grinding and drying lignite.
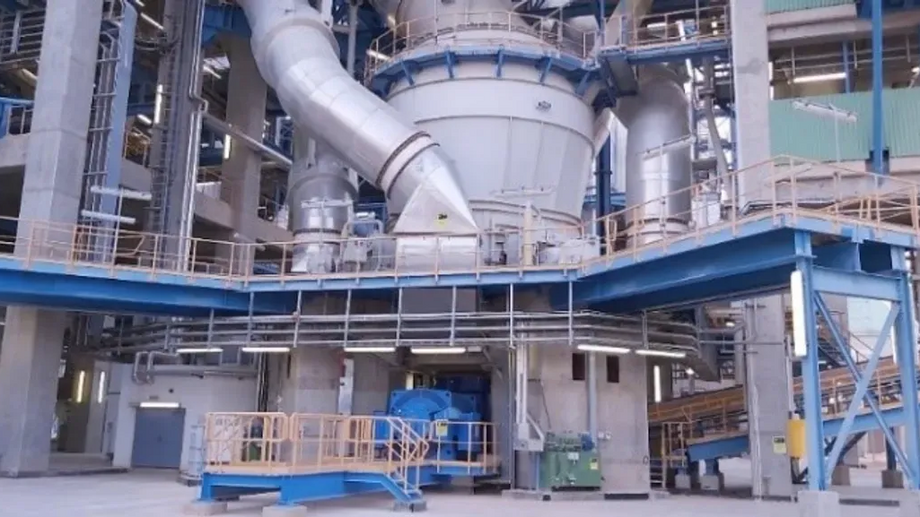
Yamama Cement
Product References: quadropol® – Saudi Arabia
Yamama Cement ordered two 10,000 tons per day kiln lines. For raw material grinding four QMR² 48/24 are contracted, while for cement grinding four polycom® high pressure grinding rolls as a combi grinding system are considered due to material properties.
The four mills are operating very successful since mid of 2021. The final set-up of the mills resulted in good operation performance. The material feed moisture is 2.61 %, which means it is fairly dry. At the end the injected water quantity, required on the table during operation, is only 0.78 %.
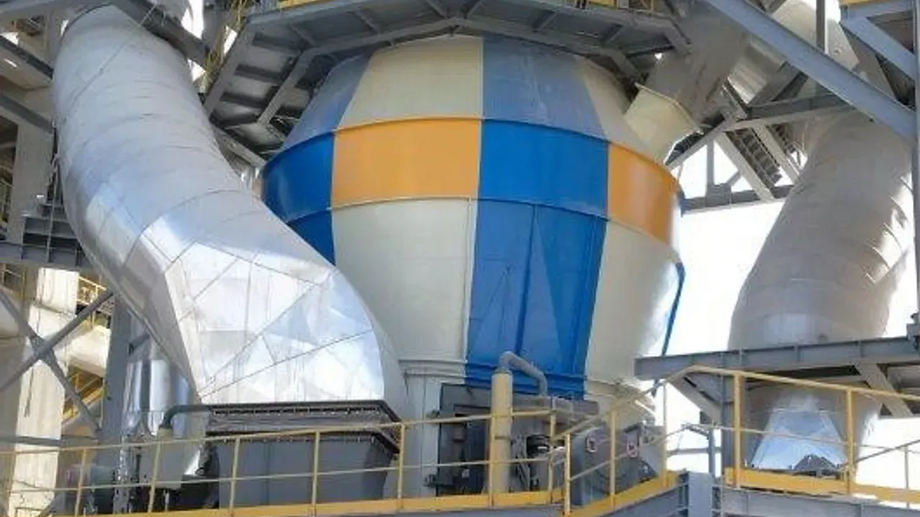
quadropol® – Turkey
Product References
The installed 4,000 tons kiln line at Afyon Cimento is successfully in operation for many years, showing truly equipment reliability and stable plant performance. For raw material grinding a quadropol® vertical roller mills QMR² 45/23 was contracted to serve the kiln line, while for cement grinding two identical QMC² 45/23 were considered for grinding different cement types. The request for interchangeable parts for the three mills was fulfilled and represents still a holistic approach. For coal grinding a QMK² 32/16 completed the grinding portfolio. The cement mills are equipped with high efficiency separators to achieve cement qualities with a fineness up to 5 000 cm2/g acc. to Blaine.